Die casting in Malaysia has grown into a significant segment of the country’s industrial and manufacturing sector, playing a crucial role in the production of high-precision metal components. As global demand for lightweight, durable, and accurately formed metal parts increases, Malaysia has positioned itself as a key hub for die casting services. The process involves injecting molten metal into steel molds or dies under high pressure, resulting in complex shapes with excellent surface finishes and dimensional consistency. This technique is commonly used in industries such as automotive, electronics, aerospace, and consumer goods, where precision and performance are critical. Malaysian die casting companies have made considerable investments in modern equipment, skilled labor, and quality assurance systems to meet the standards expected by global clients. With its strategic location, strong infrastructure, and competitive manufacturing costs, Malaysia continues to attract both regional and international businesses in need of reliable die casting solutions.
The Malaysian die casting industry is known for its use of non-ferrous metals such as aluminum, zinc, and magnesium, which are ideal for producing parts that are both strong and lightweight. Aluminum die casting, in particular, is widely practiced due to its excellent corrosion resistance, thermal conductivity, and strength-to-weight ratio. These properties make aluminum components especially popular in the automotive and electronics sectors, where efficiency and durability are paramount. Zinc die casting, while less common, is used for smaller, more intricate parts that require high precision and a smooth finish. Magnesium die casting, known for its lightweight properties, is increasingly being explored for its potential in reducing the overall weight of vehicles and electronics. The flexibility of using different materials allows Malaysian die casting companies to serve a wide range of industries and meet diverse client requirements.
One of the key advantages Malaysia offers in the die casting field is its growing pool of skilled engineers and technicians who are well-versed in modern manufacturing techniques. Local institutions and technical universities play a significant role in training workers and equipping them with up-to-date knowledge on tool design, process optimization, and quality control. As a result, many Malaysian die casting companies are able to offer services beyond simple casting, such as CNC machining, surface treatment, assembly, and testing. This value-added approach has allowed Malaysia to position itself not just as a producer of raw cast parts, but as a provider of complete manufacturing solutions. The integration of computer-aided design (CAD) and simulation tools also enables manufacturers to reduce errors, minimize waste, and improve production efficiency. These advancements have contributed to Malaysia’s reputation for delivering high-quality, cost-effective components to clients worldwide.
Environmental considerations are also becoming increasingly important in Malaysia’s die casting industry. As global attention turns toward sustainability and energy efficiency, Malaysian manufacturers are adopting more eco-friendly practices. Many companies are implementing closed-loop recycling systems, where scrap metal is reused in the production cycle to reduce waste and material costs. Efforts are also being made to improve energy efficiency by using electric melting furnaces instead of traditional gas-fired equipment, thereby reducing emissions. Water conservation, proper waste disposal, and compliance with environmental regulations are all part of the broader strategy to ensure that die casting operations are sustainable in the long term. These practices not only help companies stay competitive globally but also demonstrate a commitment to responsible industrial growth.
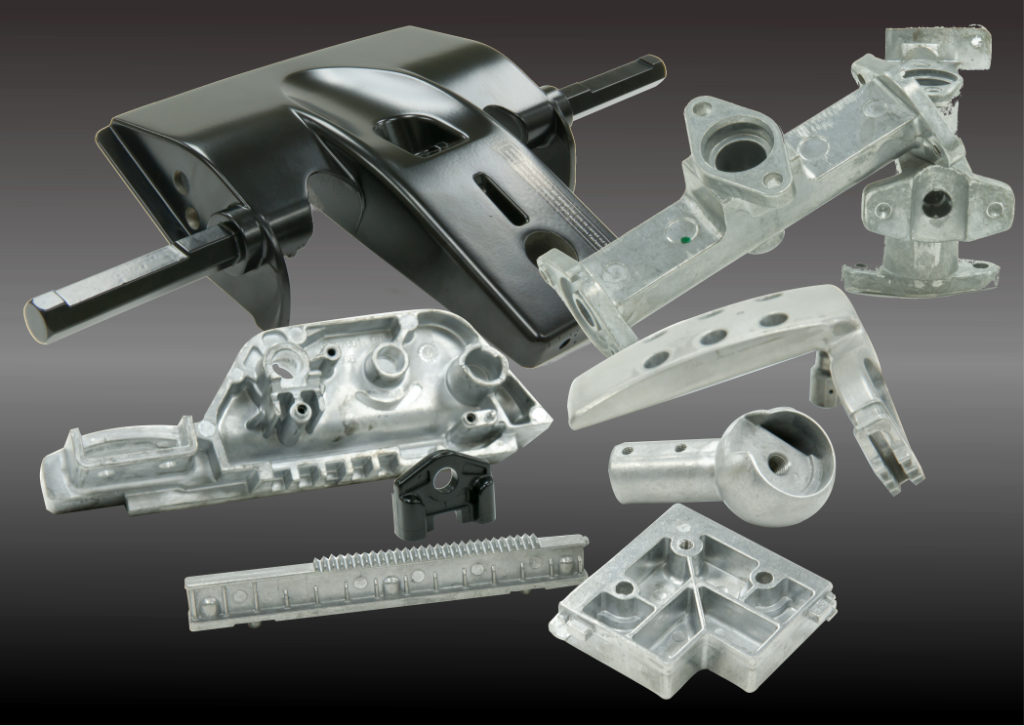
Die casting company Malaysia sector is further strengthened by its strong supply chain and logistical advantages. The country’s well-developed infrastructure—including ports, highways, and industrial parks—ensures smooth transportation of materials and finished goods both domestically and for export. In addition, Malaysia’s proximity to other major manufacturing economies in Southeast Asia allows for convenient collaboration and integration into regional supply chains. The presence of free trade agreements and government support for manufacturing investments further enhance the attractiveness of the country for die casting operations. Companies operating in Malaysia benefit from a stable business environment, transparent regulations, and access to global markets, making it an ideal location for expanding die casting capabilities. This interconnected ecosystem supports innovation, speed to market, and scalability—key requirements in the competitive manufacturing landscape.
Looking ahead, the future of die casting in Malaysia is filled with promise as the industry embraces digital transformation and advanced manufacturing technologies. The adoption of Industry 4.0 tools such as automation, IoT (Internet of Things), and data analytics is expected to improve production accuracy, reduce downtime, and enhance predictive maintenance. Collaborative efforts between the private sector and government are also being undertaken to develop smart factories and increase competitiveness. With the continued global push for electric vehicles, lightweight materials, and miniaturized components, Malaysian die casting firms are well-positioned to play a larger role in shaping the future of precision engineering. The industry’s ability to evolve with changing demands while maintaining high standards of quality and efficiency ensures that die casting in Malaysia will remain a key driver of economic growth and technological advancement in the years to come.